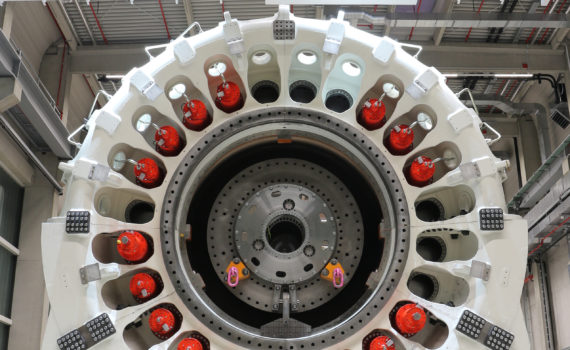
SKF eröffnet leistungsfähigstes Großlager-Prüfzentrum der Welt: Sven Wingquist Test Center offiziell eingeweiht
Category : Actuelles , Ankündigungen
In Schweinfurt hat SKF heute das leistungsfähigste Großlager-Prüfzentrum der Welt eröffnet. Die 40-Millionen-Investition soll helfen, künftige Großlager dank der Erkenntnisse aus zwei einzigartigen Testständen viel präziser und effizienter als bislang möglich auf ihre späteren Aufgaben zuzuschneiden. Zur feierlichen Einweihung der unvergleichlichen Einrichtung versammelte sich viel Prominenz aus Politik und Wirtschaft auf dem Gelände von „Werk 3“.
Im Jahr 1907 erfand der schwedische Ingenieur Sven Wingquist das zweireihige Pendelkugellager, das die Lagerung unzähliger Wellen in den verschiedensten Industriezweigen revolutionierte. Damit begründete Wingquist die weltweite Erfolgsgeschichte von SKF. „Heute, 110 Jahre später, führen wir Sven Wingquists Tradition als innovativer Technologiepionier mit einem bahnbrechenden Meilenstein fort“, so SKF Konzernchef Alrik Danielson bei der Eröffnung des Prüfzentrums. „Denn hier in Schweinfurt haben wir definitiv etwas geschaffen, das absolut zukunftsweisend ist! Es wird uns helfen, unsere Vision von einer ,Welt in zuverlässiger Rotation‘ zu verwirklichen.“
Konzentrierte XXL-Strategie
Das hochmoderne Testcenter soll Erkenntnisse zu Tage fördern, die eine maßgebliche Optimierung künftiger Großlager-Generationen ermöglichen. „Zu diesem Zweck haben wir am Standort gezielt hochqualifizierte Kompetenzen gebündelt“, so Danielson. Beispielsweise verfüge das Unternehmen in Schweinfurt schon seit 1990 über die erforderliche „XXL-Infrastruktur“, etwa in Sachen Fertigungstechnologie, Material- und Großlagertransport oder auch Verpackungs- und Versandlogistik. Hinzu kämen weitere Einrichtungen wie beispielsweise für die Generalüberholung von gebrauchten Großlagern oder das metallurgische Labor, das auf Großlager-Anforderungen ausgelegt sei. Auch wichtige Schlüsselfunktionen wie Produktentwicklung und -konstruktion sowie Kundenberatung und Anwendungstechnik für viele Großlagertypen und -kunden befänden sich „vor Ort“. „All dies resultiert aus den rund 120 Millionen Euro, die wir bereits bis 2009 in die hiesige Großlager-Fertigung investiert hatten“, erinnerte Danielson an die jüngere Geschichte des Standorts. „Jetzt fügen wir mit dem neuen Testcenter quasi den letzten ,Puzzlestein‘ hinzu, der das ‚Großlager-Kompetenzzentrum‘ in Schweinfurt komplettiert. Im Endeffekt wird die Summe all dieser Teile ein bedeutender Mehrwert für unsere Kunden in aller Welt sein: Kompaktere, robustere, reibungsärmere und langlebigere Großlager werden den Anwendern und Betreibern helfen, ihre Gesamtbetriebskosten spürbar zu senken und ihre Umweltbilanz deutlich zu verbessern. So setzen wir unsere kundenorientierte Strategie in die Tat um.“
Software zu weich für die Wirklichkeit
Um derartige Optimierungspotenziale zu erschließen, werden zwei neuartige Prüfstände die zu testenden Großlager extremen Belastungen aussetzen. „Wir betreiben diesen Aufwand, weil selbst die modernsten Simulationsprogramme immer noch nicht im Stande sind, sämtliche im praktischen Betrieb auftauchenden dynamischen Prozesse in Großlagern realitätsgetreu abzubilden“, erläuterte Dr. Victoria Van Camp, im SKF Konzernvorstand zuständig für Technologie-, Geschäfts- und Produktentwicklung. Aus diesem Grund würden aktuelle Großlager typischerweise mit „konstruktiven Sicherheitsreserven“ gefertigt – ohne dadurch vorzeitige Ausfälle gänzlich ausschließen zu können. Im realen Einsatz von Großlagern müsse es also gewisse Phänomene geben, die von den „Ursache-Wirkung-Algorithmen“ der momentan verfügbaren Simulationsmodelle nicht hinreichend berücksichtigt werden. „Solchen Phänomenen wollen wir mit unseren neuen Prüfständen auf die Schliche kommen. Das ist durchaus Grundlagenforschung – selbst nach 110 Jahren noch“, so Van Camp. Gleichzeitig solle das Prüfzentrum dazu genutzt werden, die Zustandsüberwachungstechnik des Unternehmens zu optimieren, um die „Industrie 4.0“-Aktivitäten von SKF voranzutreiben. „Die Ergebnisse werden uns in die Lage versetzen, in enger Zusammenarbeit mit unseren Kunden neue Lösungen zu entwickeln, welche die bislang existierenden Betriebsrisiken minimieren und die Potenziale künftiger Großlager-Anwendungen maximieren.“
Entfesselte Kräfte
Die handfeste Erforschung dieser Phänomene übernimmt u. a. ein gigantischer Prüfstand für Großlager mit Schwerpunkt „Windenergie-Anwendungen“. „Er ist der weltweit erste, der nicht nur ein einzelnes Hauptlager für Windturbinen unter besonders relevanten Bedingungen testen kann, sondern gleich eine komplette Lagerungseinheit; also inklusive Komponenten des Kunden“ berichtete Dr. Martin Göbel, als Manager Global Testing bei SKF verantwortlich für das Gesamtprojekt. Dabei sei der Prüfstand bereits auf Konstruktionen vorbereitet, wie sie beispielsweise für künftige Turbinen von 10 MW und mehr zu erwarten seien. Durch eine Art „Adapter“ könne er Lager mit einem maximalen Außendurchmesser von bis zu sechs Metern aufnehmen. „Außerdem kann er die riesigen Lager in alle Richtungen dynamisch mit Kräften beaufschlagen, die in ihrer Kombination um ein Vielfaches höher liegen als bei zuletzt stärksten Prüfanlage – von den deutlich höheren Test-Drehzahlen mal ganz abgesehen“, so Göbel.
Im direkten Vergleich mit dem größeren Prüfstand mag der kleinere zwar weniger „monumental“ aussehen, aber auch er habe es in sich, wie Göbel betonte: „Er treibt Großlager für Anwendungsgebiete wie den Schiffbau, den Bergbau, die Papierindustrie oder auch den Zement- und Stahlsektor an ihre absoluten Belastungsgrenzen. Zu diesem Zweck entwickelt er Kräfte von gut einem halben Dutzend Meganewton. Das ist etwa so viel wie ein einzelnes Triebwerk der Saturn V-Mondrakete!“ Dabei könne er Rotationsgeschwindigkeiten von über 200 min-1 erzielen. Außerdem könne er das zu testende Lager den denkbar ungünstigsten Schmierungsbedingungen aussetzen. „Die Analyse der daraus resultierenden Betriebszustände wird uns in die Lage versetzen, die tribologischen Wechselwirkungen zwischen unterschiedlichen Schmierungsbedingungen und verschiedenen Lager-Designs bzw. -Materialien unter hochdynamischer Belastung besser zu verstehen“, erklärte der Cheftester von SKF. „Daraus können wir wichtige Erkenntnisse gewinnen, um künftige Großlager noch viel robuster auszuführen.“
Folterknechte mit „grünem Gewissen“
Auf Basis der Test-Ergebnisse will SKF kommende Großlager-Generationen so gestalten können, dass deren Herstellung trotz ihrer größeren Robustheit bzw. trotz ihrer längeren Haltbarkeit weniger Ressourcen verbraucht. „Die enorme Leistungsfähigkeit der neuen Prüfstände hat aber noch weitere Vorteile“, wie der Geschäftsführungsvorsitzende der SKF GmbH, Martin Johannsmann, hervorhob: „Denn dank ihrer Stärke benötigen die Belastungstests nun viel weniger Zeit. Dadurch lässt sich signifikant Energie sparen, zumal wir die neuen Prüfstände mit Wärme-Rückgewinnungsanlagen ausgestattet haben.“ Aus derartigen Gründen hat das Bayerische Staatsministerium für Wirtschaft und Medien, Energie und Technologie den größeren „Stresstester“ mit rund 1,9 Mio. Euro gefördert, während der neue Prüfstand für andere Schwerindustrie-Anwendungen durch das Umweltinnovationsprogramm des Bundesministeriums für Umwelt, Naturschutz, Bau und Reaktorsicherheit mit ca. 1,6 Mio. Euro gefördert wurde. „Ich bin beiden Institutionen absolut dankbar dafür, dass sie es unserem Unternehmen ermöglicht haben, diese Pionierleistung in Deutschland zu verwirklichen“, betonte Johannsmann. „Wir begrüßen es sehr, dass die Politik im eigenen Land eine energieeffiziente Zukunftstechnologie vorantreibt, für die es einen globalen Markt gibt.“
Symbol deutscher Umweltpolitik
SKF rechnet damit, dass allein die Erkenntnisse aus dem „kleineren“ der beiden neuen Prüfstände helfen können, in den verschiedensten Anwendungen Tausende von Tonnen CO2-Ausstoß pro Jahr zu vermeiden. „Als Umwelt- und Klimapolitikerin freue ich mich außerordentlich, dass SKF hier ein ebenso innovatives wie ressourcenschonendes Projekt realisiert hat“, unterstrich die CSU-Bundestagsabgeordnete Dr. Anja Weisgerber. „Tatsächlich erfüllt es mich mit Stolz, dass Fördermittel des Bundes dazu beitragen konnten, diese weltweit einmalige Einrichtung in Deutschland anzusiedeln!“ Das sei im internationalen Zukunftsmarkt der regenerativen Energien und energieeffizienter Technologien ein bedeutender Standortvorteil. „Als globaler Vorreiter auf diesem Gebiet wollen wir die Energiewende im Einklang mit der Umwelt, der Wirtschaft und den Bürgern zum Erfolg führen – für eine saubere Umwelt bei bezahlbarer, sicherer Energie. Für diese Bestrebungen ist das Sven Wingquist Test Center ein großartiges Symbol“, meinte die gebürtige Schweinfurterin.
Aushängeschild für die Region
„Beim Spatenstich vor nicht einmal zwei Jahren hatte ich mich öffentlich dazu bekannt, dass ich Baustellen liebe“, so Schweinfurts Oberbürgermeister Sebastian Remelé (CSU). „Damals stand ich noch auf der grünen Wiese. Heute stehe ich im modernsten Großlager-Prüfzentrum der Welt. Wer sich dieses High-Tech-Monument deutscher Ingenieurskunst anschaut, wird mein Faible für solche Baustellen leicht nachvollziehen können.“ Das Prüfzentrum sei nicht nur ein klares Bekenntnis von SKF zum Wirtschaftsstandort Schweinfurt, sondern sogar ein Aushängeschild für die gesamte Region: „Denn an der Entstehung des Zentrums haben viele Firmen aus der unmittelbaren Umgebung mitgewirkt“, wie Remelé betonte. Insofern sei das Sven Wingquist Test Center geradezu ein Musterbeispiel für bayerische Innovationskraft. „Ich hoffe, dass sich das enorme Engagement, das hochspezialisierte Know-how und die unglaubliche Präzisionsarbeit, die alle Projektbeteiligten in dieses Zentrum gesteckt haben, für das Weltunternehmen SKF ebenso auszahlen werden wie für die involvierten ,hidden champions‘ aus unserer Gegend. Nicht zuletzt möchte ich Ihnen aus ganzem Herzen dafür danken, dass Sie Schweinfurts Zukunft als unangefochtenes Zentrum der europäischen Wälzlagerindustrie weiter gefestigt haben!“