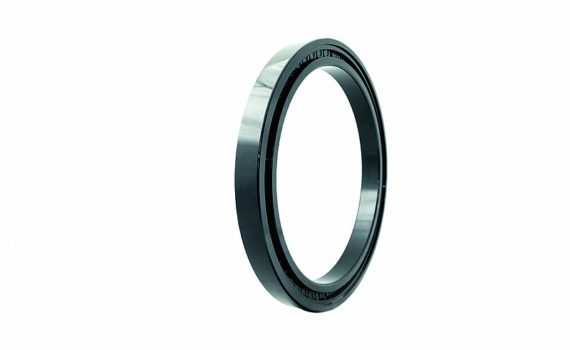
Bearings with black oxide finish – Increased performance in critical applications
Category : Νέα
At this year’s Hannover Messe in Germany, bearing manufacturer NKE Austria GmbH presents bearings with black oxide finish. The protective layer improves run-in and wear characteristics and protects against environmental effects. Especially in critical applications such as wind turbine gear boxes, black oxide finish is a cost-effective and technically viable means of prolonging the service life and performance of rolling bearings.
The black oxide finish forms a protective layer for steel parts. In a multistage chemical process, the surface layer of the treated parts is converted into a 1 to 2 micrometer thin mixed ferrous oxide layer that causes the characteristic black appearance. Black oxide finished bearing components feature a set of special technical characteristics, especially in the case of components that move relative to each other. Multiple protective effects can be achieved if only one functional element (typically the rolling elements) is treated. For best effect, however, all functional surfaces of a rolling element bearing, including the inner and outer ring as well as the rolling elements, should be black oxide finished.
Black oxide finishing is already an established method in other industries. NKE uses this technology to further improve the technical properties of rolling bearings. The method has proven itself in practice especially with full complement cylindrical roller bearings, but other types of rolling bearing are also black oxide finished, depending on the application. NKE offers a large number of black oxide finished rolling bearings. At NKE, this finish is used especially for cylindrical roller bearings, which then carry the suffix SQ94. The most common variants are SQ94B (rolling elements black oxide finished) and SQ94-D (all bearing components except for the cage black oxide finished).