The mechanism of surface rolling contact fatigue in rolling bearings is investigated by means of dedicated experiments and numerical simulations of the damage progression.
Rolling contact fatigue (RCF) is a typical failure mode in rolling bearings and similar types of machine components. The fundamental work in RCF is due to Lundberg and Palmgren [1], [2]. The Lundberg-Palmgren theory was mainly focused on subsurface rolling contact fatigue, and it relies entirely on ideally smooth Hertzian stress calculations. Surface rolling contact fatigue (SRCF) instead involves the area close to the surface of the contact (a few microns deep) that is strongly affected by local surface traction and stresses originated from geometrical features of the surface such as roughness, profile deviations, indentations, etc. The interaction between the elasto-hydrodynamic lubricating (EHL) film and the actual features determining stress risers at the surface is very important in the understanding of surface fatigue phenomena of rolling bearings (Morales-Espejel and Gabelli [3]). In this article, the progression of SRCF is investigated by modelling the contact and the interaction with deviations of the surface micro-geometry that generate stress concentrations. Comparison of the numerical simulations with a set of experimental results indicates good correlation, allowing the formulation of a hypothesis about the underlying mechanisms of SRCF, as well as its inception and growth in rolling bearings. This new knowledge fits very well with the basic idea behind the SKF Generalized Bearing Life Model (GBLM) that separates surface from subsurface fatigue damage [4][5].
Theoretical investigations in damage progression
Often, rolling contact fatigue damage originated around surface microgeometry features develops into a spall. Spall propagation, in its advanced form, is strongly influenced by macrogeometry aspects – for example, the evolution of the raceway contact geometry and resulting overall stress field in a rolling bearing. Several researchers have studied spall propagation in rolling bearings in the attempt to associate the mechanical aspects driving the damage progression.
A recent investigation carried out by the present authors [6] has studied SRCF propagation of predented rolling bearings, both with a model and experiments, concluding that the mechanisms involved in ball bearings require the consideration of lubrication conditions and the interaction of stresses between the surface and subsurface to understand the development of the typical V-shaped cracks along the raceway, differently from the initial transverse damage growth observed in roller bearings that can be explained sufficiently with only dry contact assumptions.
Experimental observations in damage progression
Snare [7], in his statistical analysis of bearing reliability, monitored the propagation of a spall in a cylindrical roller bearing, showing the clear progression of the damage across the raceway before the spall starts to propagate along the raceway. Fig. 1 shows the experimental tests of Snare.
Current understanding
From the theoretical and experimental investigations found in the literature, at least two distinctive spall propagation phases from surface defects are clearly recognized. The first one is when the spall grows across the raceway at a more or less slow rate, and the second is when it grows along the rolling path in a more accelerated fashion. The reason for the across-raceway propagation of the spall, in its initial phase, is understood as a consequence of the higher stresses present at the diametral edges of the spall – that is, along the direction orthogonal to rolling, compared to the stresses at the spall leading and trailing edges.
The behaviour of the spall inception and propagation on ball bearings (fig. 2) and roller bearings (fig. 3) is strikingly distinct. Surface-initiated spalls in ball bearings initially develop with a characteristic V shape at the trailing edge of the indentation, rapidly growing in the rolling direction with the detachment of raceway material from the V-shaped area. The growth of the spall is observed in the rolling direction, which is the direction opposite to the direction of friction and slip present at that location (fig. 2). Surface-initiated spalls in roller bearings initially propagate at the two sides of the original initiation spot, growing across the raceway before expanding along the raceway (fig. 3).
The objective of this article is to shed further light on the progression of surface-initiated fatigue damage of roller bearings. This is to understand via modelling the driving mechanisms behind the damage propagation as observed in the experiments, as a continuation of the work reported by the authors [3], on the initial damage phase, but now focused of the propagation of this damage.
Experimental work
Experiments were conducted on standard tapered roller bearings; see table 1.
Tapered roller bearings were artificially indented using an indentation load of 1,250 N and a 1 mm diameter tungsten carbide ball indenter. This load provided dents with a diameter of 400 µm, 30 µm dent depth, and a raised edge height of about 2 µm. The experiment consisted of eight equally spaced indentations around the circumference on the inner ring of the tapered roller bearings. The dents were also spaced at 0.5 mm steps across the raceway, starting from the raceway edge. However, in this article, only the progression of damage of the dents located at the centre of the raceway will be discussed in detail. Under the operating conditions given intable 1, the axial load provided a Hertzian width in the rolling direction of about 142 µm, which is substantially narrower compared to the dent diameter. The experiments were run at different numbers of revolutions to observe the progression of the fatigue damage, resulting from the stress concentration and lubrication conditions of the dents.
Fig. 4 shows some experimental results about the progression of the dent spalling in the tapered roller bearing for an increasing number of revolutions. The spall initiated at one side of the dent and then progressed towards the two sides of the dent across the raceway – that is, along the direction orthogonal to rolling. In fig. 4(b) an approximated contact ellipse was drawn for comparison with the final spall. Several inner rings were monitored by periodic microscopic inspection performed on each bearing, at about 5 million revolutions apart, to detect the initiation and propagation phase of the spall. Each dent was microscopically inspected and photographed as a function of the number of revolutions performed in the test. The initial development and further progression of the spalled area around the dent were measured by digital image processing of the collected microphotographs from several individual dents. The results of this detailed investigation provided very precise information about the initial and progressive growth of the spalling damage area against number of revolutions.
All the data collected from the six individual dents that developed spalling damage are shown infig. 5.
A more detailed inspection of the average test data indicates that the progression of the spalled area follows a three-stage process:
1. The incubation time of 50 to 60 million revolutions in which no apparent visible damage can be detected in the bearing raceway; this is about the fatigue rating life of the bearing.
2. The initial damage progression phase, which extends for 30 to 40 million revolutions, as expected, displays an exponential growth of the damaged area.
3. The accelerated growth. This extends for 20 to 25 million revolutions, during which the growth rate substantially increases (more than twice compared to the previous period).
Damage propagation model
Calculation of the damage in the rolling contact is carried out by modelling in the first instance the initial indentation of the raceway. This is done using a parametric analytical function that closely reproduces the shape of the actual dent.
The dent geometry is then included in an overrolling contact model to reproduce the Hertzian cycling stress of the actual test bearing. The damage progression calculation is performed using the basic surface fatigue and detachment model developed previously by Morales-Espejel and Brizmer [8] and fully described there. However, some modifications and adaptations were also introduced. For instance, the routine for wear calculation, as described in [8], was switched off to accelerate the speed of the numer-ical simulations. The fast lubrication model is switched off, and only the dry contact model is used for situations where the initial indentation is wider than the Hertzian contact in the rolling direction, which is the case for the simulated tapered roller bearing of fig. 4(a). The model is then used in the calculation of the overall pressures and stresses. This approximation is valid because in this case the lubricant is likely to escape from the dent and contact. No generation of hydrodynamic pressure is to be expected at the dent edge region whose pressures can therefore be modelled using the dry contact hypothesis (for ball bearings with wider Hertz contact area, the lubrication model cannot be ignored).
Once the contact pressures are calculated, the stress history is obtained for a series of time steps designed to simulate the passage of the indentation through the rolling contact (see [5]). From this multistep simulation process the fatigue stress history can be computed for further processing by the fatigue criterion in order to estimate the fatigue damage accumulated from the start to the current load cycle. This scheme follows exactly the same data processing introduced by Morales-Espejel and Brizmer [8]. The total damage accumulated up to the current load cycle is calculated following the Palmgren-Miner rule.
When fatigue reaches a critical damage value, the possibility of an onset of material fracturing emerges. The current scheme does not have a detailed crack propagation model; the damage propagation is simulated by simply removing fatigued material. For this purpose, a simple material detachment model [8] was implemented that performs the task of removing the material with accumulated critical damage and material above it. This model contains also a threshold depth (h) from the surface below which material with critical damage is not allowed to detach. This threshold depth can be set up from h = 0 to h = ∞. Setting h ≥ 0 will allow material below the surface to detach. The current model cannot give a precise indication of the damage growth if the parameter h is not known in advance or if some experimental results are not available, but it can very well describe damage growth ranges as will be shown below. The calculation process is repeated for a given number of load cycles (up to a maximum, typically > 109 overrolling cycles), after which the damage progression history is reported.
Model results
Test data are given in table 1. In this case the dents are wider (i.e., diameter 400 μm) than the Hertzian contact in the rolling direction (i.e., 142 μm); therefore, it will be impossible during overrolling to develop the required EHL pressure over the dent. This will induce a collapse of the oil film at the edge of the dented area. Under these conditions, the effect of the lubricant film can be excluded from the analysis, and the progression of damage can be simulated simply using the dry-contact approximation.
Fig. 6 shows the spall evolution from the initial indentation for an increasing number of revolutions; they also show the progressive changes of the Hertzian pressure and related subsurface stresses. The results of the numerical simulations clearly show the preferential direction of the progression of the spalled area. The damage starts from the dent lateral edges and progresses in the axial direction across the raceway in a similar manner to the one observed in the experiments (see fig. 4). By computing the area covered by the damage and its evolution with the number of bearing revolutions, it is possible to obtain the curve of the progression of the damage area versus number of revolutions of the bearings. This was computed for two threshold depth levels, h, a minimum and a maximum to characterize the scope of the model simulations (hmin just touching the area of maximum orthogonal shear stress around the dent and hmax well beyond that). The resulting damage progression curves are shown with dashed lines in fig. 5. A thin dashed line is the result of the most conservative setting for the estimation of surface-initiated microspalling – that is, minimum value of the threshold depth. Therefore, the simulated results represent a safe bound of the damage, defining the conditions for the maximum expected damage area from any surface-initiated spall.
With the implementation of a maximum threshold depth value, h, the evolution of the damage shown in fig. 5 with a thick dashed line shows a more realistic match with the experimental results. Noticeable is the initial trend of the computed damage area, which shows a stepwise progression clearly matching some of the experimental measurements. This trend achieves a stable growth rate of between 90 and 120 million revolutions; this interval can be compared to the measured initial progression phase of the damage growth of the dent as discussed in the section “Experimental work”.
Fig. 7 shows the damage growth rate of the experiments compared to the one obtained from the numerical simulations, which is 11.5 million revolutions (134 million cycles). This good correlation between the average of the experimental results and the numerical simulations shows the ability of the computation to capture some principal effects of the surface fatigue mechanisms and of the initial spalling progression. In addition, the experimental results indicate an accelerated growth after 100 million revolutions that seems absent from the results of the numerical simulations. A possible explanation of this behaviour is that the generation of a spalled area also results in additional loads due to the dynamic response of the bearing to the spalling damage. At the moment, these additional loads are not included in the model; thus, only the initial spalling damage can be reasonably compared with the numerical
simulations.
In the simulated results the mechanism of the damage progression is also interesting. Because the indentation is a bit larger than the Hertzian width in the rolling direction, the most loaded zone in the raceway is the lateral area of the indentation, where the damage indeed will initiate and progress. This propagation mechanism can also be found in the numerical simulation showing the lateral edge of the spall affected by the largest surface pressures and subsurface stress concentrations (fig. 6). This type of spall propagation seems to be typical of roller bearings.
Discussion and conclusions
Experiments have been carried out on tapered rolling bearings. The raceways of the bearings were indented with predefined hardness imprints. This created a series of surface stress risers from which surface spalls were originated, allowing the detailed study of their inception and progression. An existing model for surface microgeometry fatigue (Morales-Espejel and Brizmer [8]; i.e., surface distress) was adapted to study the surface-initiated macro-spalling process.
The model was applied to gain better insight into the initiation and early propagation phase of the spall. From the computational results it is found that indeed the numerical model can simulate and explain well many of the experimental observations; in particular the experimental results have indicated that in case of the tapered roller bearing, the spall propagates initially across the raceway – that is, along the direction orthogonal to rolling. In general in line-contact bearings, the stresses are higher at the lateral edges of the indentation. These higher stresses drive the growth of the spall across the raceway during the initial expansion of the spall.
From the results of the current work, the following conclusions can be drawn:
1. Pre-indented roller bearings propagate spalls initially across the raceway, driven by the higher stresses found at the edges of the spall along the direction orthogonal to rolling, as previously described in the literature.
2. The presented model describes well the two spall propagation mechanisms. For roller bearing spalls in particular, a good correlation between the model prediction and the experimental measurements is found in the initial spall growth rate.
Acknowledgment
The project was partially financed by the European Commission Marie Curie Industry-Academia Partnerships and Pathways (IAPP) – iBETTER Project.
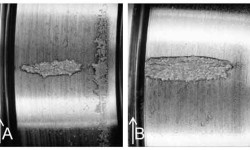