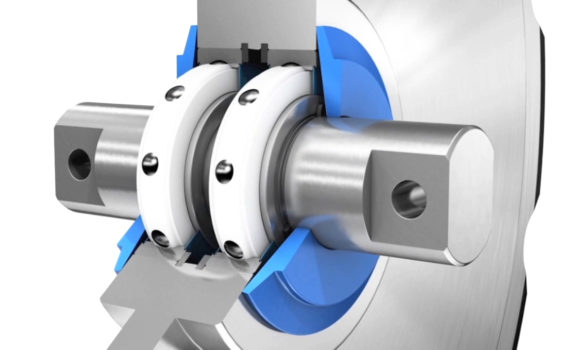
Why hygienic design of bearings is key to food safety
Category : News , Technical Articles
An emphasis on the hygiene element of the design of equipment can play an important role in controlling the safety of food products manufactured. However, applying this too broadly without focussing specifically on the hygienic design of the components part of the system, can potentially risk the spread of bacteria trapped within bearings, says Davide Zanghi, the person responsible for the Hygienic design office in SKF.
Hygienic design considers specifically how problems such as corrosion, lubricant leakage, cleaning and self-drying could adversely affect food safety – and applies design principles to solve the problem. In essence, it is a design philosophy applied through dedicated and specific rules. Just as ergonomic design pays close attention to the physical needs of product users, hygienic design has a laser focus on preventing issues of food contamination.
The European Hygienic Engineering and Design Group (EHEDG) aims to promote safe food by improving the standard of hygienic engineering and design, and includes equipment manufacturers, food companies and research institutes among its members. In November 2016, in Denmark, it ran its biennial World Congress. On this occasion, SKF – an EHEDG member since 2006 – highlighted its long record using these design principles.
Design principles – a dim view on bearing components
In general, EHEDG guidelines consider bearings an easy place to trap food particles and water and therefore these are seen as potential breeding grounds for harbouring bacteria. The advice is: keep bearings well away from food product contact areas.
This is very much the case with recent guidelines on hygienic design of belt conveyors for the food industry, where EHEDG addresses two of the major challenges in safe food production: how to avoid contamination of food through inadequately designed processing equipment and how to improve food safety without raising operating costs for cleaning and production hygiene. Even if lots of attention goes on systems design and major components such as belts; bearing and bearing units consistently have a low profile within the overall hygienic system design.
However, even if not in direct contact with the food zone, bearings are often in the proximity of food product and with high pressure water or dry cleaning regimes they pose the risk that bacteria – if present – can get airborne and potentially contaminate the food product.
In order to minimize the risk of contamination, designing bearings with hygienic design principles in mind is a key consideration. One of the most important principles underpinning hygienic design is the ability to clean effectively. This may be easy to understand, but it is often difficult to achieve in practice, for bearings and bearing units. For a start, the products should be made from non-corrosive and non-porous materials, such as stainless steel, or composites and with shapes that are cleanable, allowing self-draining. Bearing units should have filled bases, which removes cavities where germs may fester.
In general materials used such as elastomers and composite and grease should be compliant with food safety directives and regulations. In all instances, potential of grease leakage onto the food product during operation should be avoided.
Ideally, bearing units should have effective end covers – that prevent process contaminants and cleaning fluids from entering the bearing units cavity and, at the same time, allow a frequent visual inspection.
Other relevant areas are:
• avoid metal to metal contacts in between unit components and in between units and attaching surfaces
• avoid re-lubrication as much as possible
• achieve high service life despite of very demanding operating and cleaning regimes
Hygienic design applies to food production and packaging machinery in its entirety. But dealing specifically with one of the most problematic components – bearings – can only help to improve the overall risk strategy.